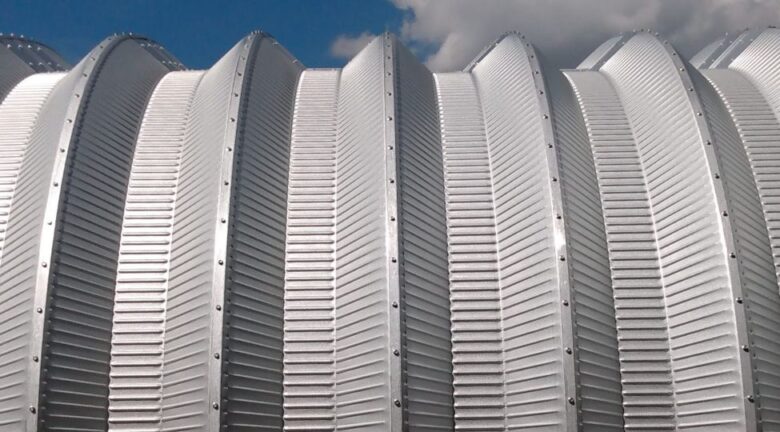
Engineering
Engineering Standards For Metal Arch Buildings
Despite its simple shape, extensive engineering goes into creating Quonset huts that withstand high winds, blizzards, floods, fires, earthquakes and whatever else the environment can throw at them.
Chances are if you’re interested in buying a Quonset, you want it to be an investment that can last a lifetime. We’ll cover the biggest engineering factors that impact the strength and long-term durability of your Quonset hut and the right questions to ask when shopping for the perfect building.
Quonset huts can be designed to meet local, FEMA, and International Building Code (IBC) construction standards but only if they are properly engineered. The differences between a fabric, wood or aluminum building and a steel Quonset hut are vast, with steel being superior in key areas:
- Grade of steel
- Gauge of steel
- Corrugation depth
- State-stamped blueprints
- Fasteners and hardware
- Protective coating
- Arch shape
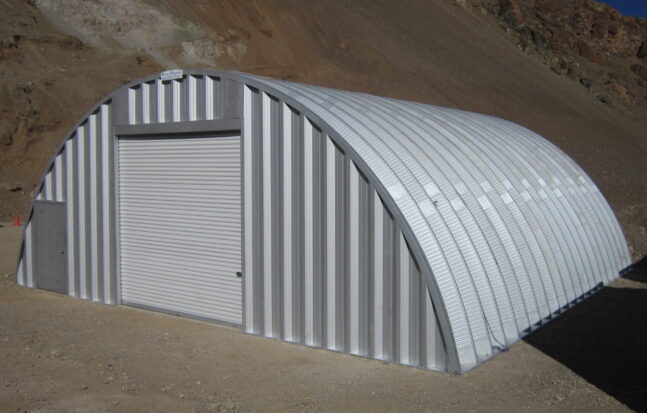
Grade Of Steel
Not all steel is created equal. Lower grade or lower quality steel is weaker in both yield and tensile strength. The higher the steel grade, the more resistant it is to bending, flexing or warping during construction and over time.
Most steel buildings use one of three grades of steel, 40, 50 or 80 grade. Different organizations like ASTM, SAE, and AISI grade steel based on several factors including things like:
- Chemical composition: Amount of carbon and other alloying elements (such as manganese, silicon, nickel, and chromium) in the steel.
- Mechanical properties: Yield strength (PSI), tensile strength (PSI), elongation (percentage), and hardness (scale specific).
- Production differences: Variations in production methods, heating, and cooling processes
These factors work together to control the formation and distribution of key microstructural components, such as ferrite, austenite, cementite, and pearlite, which ultimately determine the steel’s strength, hardness, ductility, and grade.
Grade | Yield Strength (psi) | Ultimate Tensile Strength (psi) |
40 | 40,000 | 60,000 |
50 | 50,000 | 65,000 |
80 | 80,000 | 82,000 |
Buying Question: Cheap steel buildings often use 40 grade steel, so always ask the grade of steel being used as part of the pricing. Higher-grade steel is stronger, more durable, and better equipped to withstand heavy wind and snow loads
While tin and aluminum alloys may have a lower upfront cost, they are far less durable than steel, lasting fewer years and often requiring frequent maintenance.
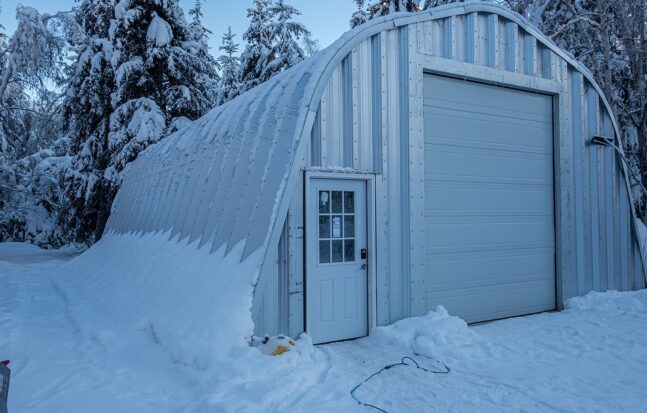
Gauge of Steel
Gauge measures the thickness of steel and other metals, with lower numbers indicating thicker material. For Quonset huts, steel gauges typically range from 12 to 26. Going much thicker can drive up costs, while going much thinner may reduce the benefits of using steel over a cheaper alloy.
Consider a thicker gauge of steel if:
- Building is intended for long-term use.
- Building projectile impact ratings are needed.
- High wind ratings are required.
- Snow loads are a concern.
- Regular seismic activity is present.
- You are storing high-value items.
When discussing steel gauge, nominal thickness and minimum thickness are key distinctions that impact durability, performance, and compliance with industry standards.
- Nominal Thickness refers to the standard or theoretical thickness of the steel as defined by manufacturers and industry specifications. It represents an approximate value rather than an exact measurement.
- Minimum Thickness is the lowest acceptable thickness that a steel sheet can measure and still meet quality standards. This accounts for production tolerances, ensuring the steel performs as expected under load.
Buying Question: Always consult with a state-licensed engineer or architect about the proper gauge of steel. Ask what gauge of steel is appropriate for your code and load requirements. Go with a lower gauge steel if you live in an area that may see extreme weather events, such as natural disasters or severe storms. Gauges thinner than 22 may not be suitable for long-term applications and will have a shorter lifespan.
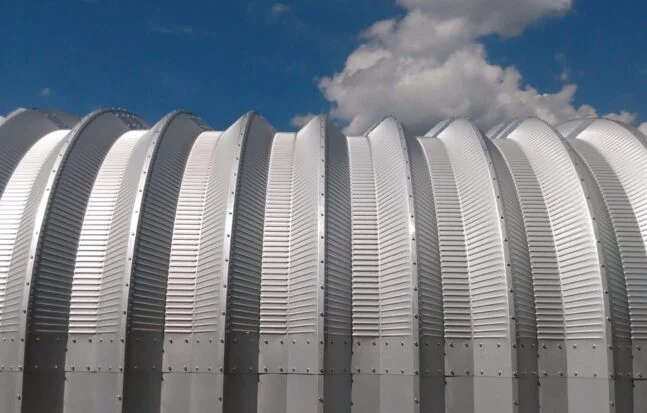
Corrugation Depth Of Arches
Corrugated steel has long been a popular choice for commercial and agricultural buildings and is gaining traction in residential steel construction. Much like how a cardboard box gains strength from its wavy inner layer, steel sheets become significantly stronger when corrugated into ridges and grooves.
Corrugated and ribbed steel panels are typically formed into waves, ridges, or square-edged patterns. These sheets are manufactured using a cold-forming process, where the metal is first pressed flat and then shaped through roll forming. During this process, the sheets are cut to length and then passed through rolling dies to create the corrugations.
While corrugation requires slightly more material during production, the added durability it provides to a Quonset hut is well worth the investment. From a structural engineering standpoint, corrugation offers several advantages for meeting code and load requirements, including:
- Increased lateral stability
- Improved shear strength
- Enhanced stiffness
- Higher load-carrying capacity
Engineer Buying Question: Shallow corrugation saves the manufacturer production costs, but results in a weaker building. Ask about the corrugation depth of your Quonset arches. For maximum strength, avoid non-corrugated panels and ensure the corrugation depth is at least 7.5 inches.
State Stamped Blueprints
Most buildings require a permit to be built and will need some sort of insurance. To streamline the permitting process and simplify insurance applications, drawings reviewed, approved, and officially stamped by a state-licensed professional engineer or architect are often used.
These are known as state-stamped blueprints, which ensure code compliance and quality assurance.
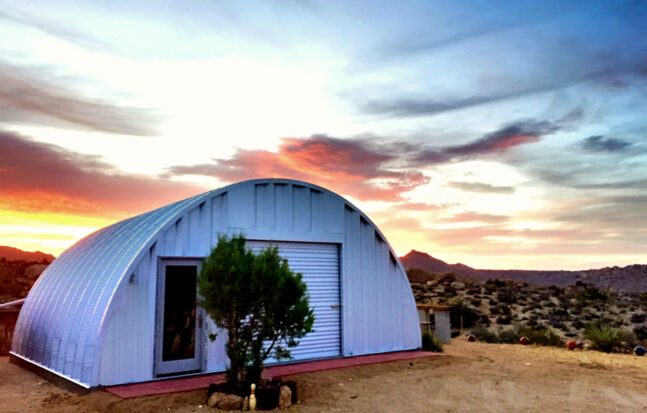
Compared to basic AutoCAD renderings, state-stamped blueprints have greater detail that clearly defines your building’s engineering design. This includes details such as:
- Precise measurements and dimensions
- Front, side, and rear elevations
- Foundation plans (only if needed)
- Construction details and materials to be used
- Specifications for snow loads, wind resistance, and seismic conditions
- Arch profiles showing correct placement of arch panels and gauge thickness (for metal buildings)
- Arch reactions
- Design report (only if needed)
This level of detail makes permit approvals smoother and provides insurance companies with clear documentation that the building meets code and load requirements.
Engineer Buying Tip: Before you buy any metal building, ask if you will be provided blueprints stamped by an engineer who is licensed in your state. Some steel building companies offer basic AutoCAD renderings or “factory-stamped blueprints,” which can look nice and communicate the basics of building, but may not be sufficient for permitting and more difficult to obtain insurance for.
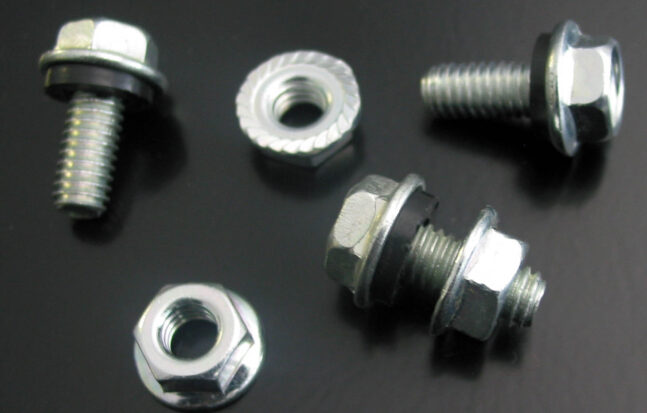
Nuts, Bolts & Washers
A Quonset hut’s incredible strength doesn’t come from just the steel arch panels, it’s also the nuts and bolts that fasten the panels together and secure them to the foundation.
Basic or cheap nuts and bolts will come loose over time or have a shorter lifespan because of three main factors:
- Nut and bolt grade
- Chemical protective coatings
- Washer type
Nut & Bolt Grade
Nuts and bolts are graded on their tensile strength, chemical makeup and functionality. Grading is done according to industry standards set by organizations like the SAE, ISO and ASTM. Nuts and bolts that are ungraded are cheaper to produce but are reserved for smaller applications that don’t need to consider the specified strength of the fastener.
The best nuts and bolts for Quonset huts include:
- Grade 5 locking nuts: Made from quenched and tempered medium carbon steel with a minimum tensile strength of 120,000 psi.
- Grade 2 bolts: Made from low or medium-carbon steel, tensile strength ranging from 60,000 to 74,000 pounds per square inch (psi).
Hex head nuts and bolts are preferred because they resist stripping and provide better torque transfer when drilled. Additionally, locking nuts are used because their serrated bottoms grip the steel during installation, creating a more secure connection.
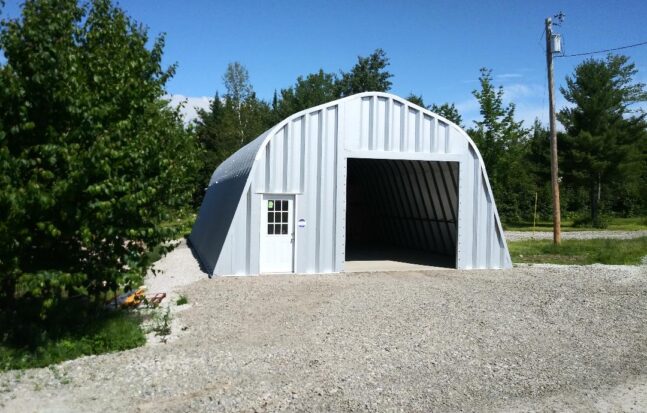
Nut & Bolt Coating
Because Quonset arches are designed to last well over 50 years, their nuts and bolts must have a protective coating that matches that level of durability.
While almost all nuts and bolts have a coating, there is a vast difference between these coatings and how they impact the longevity of the hardware.
The most popular Quonset nut and bolt coatings are:
- JS500: Basic/lower quality, designed for temporary or farm use
- 500 hours of corrosion resistance in salt spray tests
- Considered a standard coating for hardware
- JS1000: Used for higher-end applications for a longer duration
- 1,000 hours of corrosion resistance in salt spray tests
- 20-25 times the corrosion resistance of regular electro-zinc products
- NZF3000S: Best available coating, longest-lasting, construction-grade
- 3,000 hours of rust-free performance in salt spray tests
- Outperforms hot-dip galvanizing by 5 times and electro-plating by 60 times
- Considered a significant upgrade from JS and DT coatings
- Uses a zinc and aluminum flake coating process
For Quonset huts, the best chemical coating by far is the NZF3000. It outperforms other options and can be guaranteed to last for over 50 years.
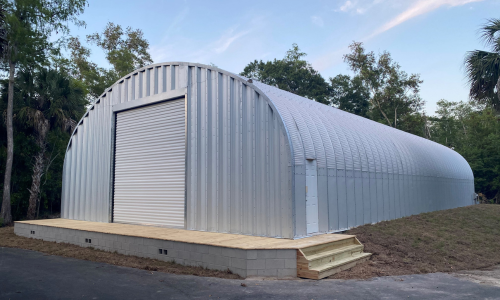
Washer type
No matter how strong your nuts and bolts are, if you use a standard neoprene washer your Quonset’s longevity will suffer.
Neoprene rubber washers shouldn’t be used in Quonset construction because they are affected by temperatures and exposure to water, causing cracking and creating weak points in your building.
Instead, a premium Low Density Polyethylene (LDPE) is used.
LDPE Advantages:
- Industrial grade plastic
- Zero water absorption
- Cleared for temperatures between -210°F and +185°F
LDPE washers are also resistant to a wide range of chemicals and are more flexible than neoprene, all while being cheaper to produce than standard neoprene washers.
Engineer Buying Tip: Always use the highest-grade hardware available for your building. Avoid low-quality alternatives, such as ungraded hardware with JS or DT coatings and rubber washers. Ask for details on the grade of nuts and bolts, protective coatings, and available washer types to ensure long-term durability.
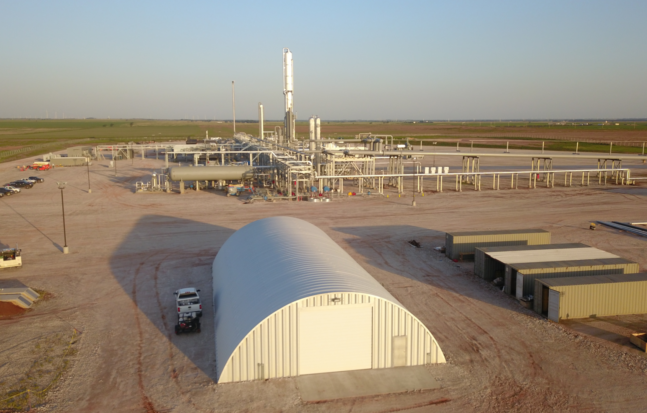
Steel Protective Coating
Since steel is primarily composed of iron, and untreated iron naturally rusts, having an anti-corrosive coating on your Quonset hut is essential. A protective coating prevents rust, enhances durability, and shields the building from environmental damage.
Every new Quonset hut looks great when first built, but the key to keeping it that way for decades is using the best available rust-inhibiting coating. Two main factors determine the effectiveness of protective coatings: how thick the coating is and its chemical makeup.
Most Quonset manufacturers offer coatings that range between AZ50 and AZ60. Thinner coatings, such as AZ50 and AZ55 are used for projects where the formability of the steel is more of a concern than durability. While all of these coating thicknesses are used in construction, AZ60 coating is the thickness and is best for Quonsets because the steel will be in direct contact with the outdoor environment, and the lifespan of the building is beyond 50 years.
- AZ50 (AZM150): Thinnest coating with the most limited warranty and lifespan
- AZ55 (AZM165): Good for certain projects, but not recommended for home or business use
- AZ60 (AZM18O): Best available, thickest coating with the longest lifespan
In the 1980s, an improved formulation of Galvalume was invented alongside steel production techniques that created stronger steel with a dry Galvalume coating known as Galvalume Plus. Galvalume Plus is better than its predecessor in every way possible.
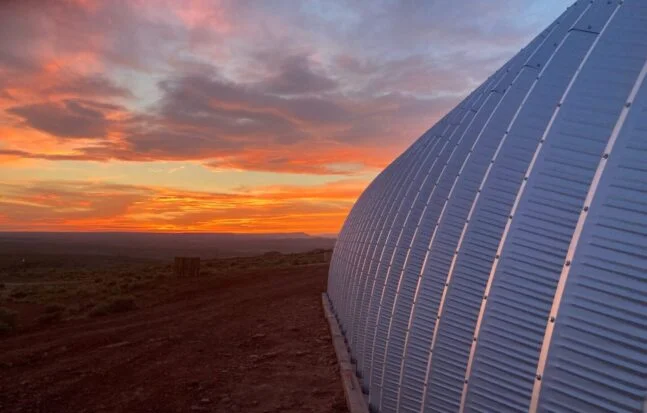
Galvalume Plus Benefits:
- Superior corrosion resistance: 2-4 times better resistance to corrosion than traditional galvanized coatings of similar thickness.
- High heat reflectivity: This makes buildings more energy-efficient and comfortable. Quonsets are Energy Star-rated.
- Long lifespan: It can be expected to last many decades before requiring maintenance, no matter the environment.
- Excellent cut-edge protection: The aluminum-zinc alloy coating prevents corrosion at exposed edges better than standard galvanized steel.
- Easy handling: Oil-free finish that’s dry to the touch, no need for gloves or rags to touch the steel.
- No maintenance: Stain, blemish, and smudge proof for 50 years.
Galvalume Plus is hot-dipped and applied using reverse roll coaters. Then, it is thermally cured so the coating stays on the steel and provides long-lasting protection against rust for decades, that’s smudge-proof.
This allows the Galvalume Plus to protect the steel by acting as two types of coatings, barrier coating (physically separating the metal from corrosive elements) and sacrificial coating (reacting with the corrosive agents). This dual protection increases the longevity of the steel for many decades.
Engineer Buying Tip: Ask what thickness and type of protective coating is available. Insist on using the thickest protective coating available, AZ60, and only the newest formulation of Galvalume, construction-grade Galvalume Plus.
Arch Shape
The shape of your Quonset arch will impact the overall strength of your building. Modern steel Quonset buildings can vary the pitch of the wall and roof segments to form four different arch shapes:
For most applications, the shape of the arch will be a choice based on the look and pricing, however, instances with special code and load requirements may prohibit certain models from consideration.
The strongest arch shape is the X-model because of both its pitched roof and walls that spread the weight or force on the building more evenly. If you live in Alaska or a place with high snow loads, you should consider a Quonset with a 4:12 pitched roof like an X-model.
Engineering Buying Tip: You can make sure you’re meeting your area’s minimum code and load requirements or not paying extra for over-engineering you don’t need by getting specific details on the wind and snow rating of your building to determine the correct arch.
FAQs
How do I get engineering specs for my building?
When purchasing a Quonset, always work with an experienced team that can provide you with engineering details through a state-stamped blueprint. Within your blueprint will be renderings of your Quonset and the building specifications you’ll need to submit to the permitting office and any insurance.
How do I know my area's code and load requirements?
Your county or relevant permitting body typically publishes their building codes online. You’ll need to pay attention to the code and load requirements based on your building’s application and current zoning. Residential, commercial, and rural building codes may differ, so be sure to consult a state-certified engineer or architect for final review.
Why build a Quonset hut out of steel? Why not fabric or aluminum?
An arch building can technically be made out of almost any metal, but for strength, longevity, and low maintenance, modern Quonset huts are exclusively made out of steel that’s coated in an anti-corrosive agent to protect against rust.
Steel is stronger and lasts longer than fabric, wood or aluminum. We cover why steel is better than other buildings here:
Are steel anti-corrosive coatings oily or dry to the touch? Do they smudge?
If a coating is not thermally cured, it is more than likely going to feel oily to the touch and is more likely to smudge and show fingerprints. Galvalume coating is an example of this.
Dry finish organic coatings like Galvalume Plus provide excellent resistance to smudging and can make assembling your steel building easier, as they won’t get any residue on your hands.
This also makes assembly safer, as slippery panels are more likely to fall out of your hands and can be more dangerous while working on the roof of buildings.